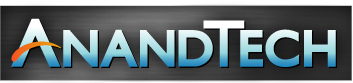
Original Link: https://www.anandtech.com/show/437
Heatsink Guide - The Basics of Cooling & Heatsink Technology
by Tillmann Steinbrecher on January 5, 2000 12:02 AM EST- Posted in
- Guides
Back in the days of 486 CPUs with clock speeds of up to 50 MHz, PC processors got along fine without any cooling devices, and nobody paid much attention to CPU cooling. The first x86 CPU in which a heatsink was recommended (but not necessarily required) was the 486DX2-66. Over the years, the power usage of CPUs has been increasing constantly, and today, where even many graphics chips need coolers, a CPU without a heatsink is unthinkable. Reason enough to have a closer look at the technology behind heatsinks!
The Physical Effects
To make it simple, a heatsink is nothing else then a strangely formed piece of metal. How does it dissipate the heat generated by the CPU?
Well, there are three ways how an object can get rid of heat: Radiation, conduction, and convection.
Radiation, as the name suggests, means that the heat is simply radiated away from the object, through electromagnetic radiation (photon transport). This effect is not bound to gas or other substances surrounding the heatsink. Radiation will even take place in a vacuum. How well an object can radiate heat depends on the material and the color (black is best). See fig. 1 for an illustration.
Conduction is the exchange of kinetic energy between molecules. Less energetic (lower temperature) particles gain kinetic energy by colliding with more energetic particles (through physical contact). Since direct contact is required, a heatsink (surrounded by air) cannot get rid of heat using conduction. However, conduction is the effect that's responsible for the heat transfer from the CPU to the heatsink.
Convection is heat transfer by movement of a heated substance (gas or liquid). This means that the heat is transferred to the molecules of the gas (or liquid) surrounding the hot object, and then transported away through movement of molecules. If the gas or liquid around the object is forced into movement (e.g. by a fan blowing air across a heatsink), then we're dealing with forced convection (see fig. 2).
Forced convection is the effect that's mainly responsible for the cooling capabilities of a fan-heatsink combo. When a CPU cooler cools a CPU, most heat is dissipated by forced convection, and only in very, very small part by radiation.
In order be efficient, a heatsink must be designed in a way that it will take advantage of this effect. There are two ways to achieve this goal:
- Make the surface area of the heatsink as big as possible
- Provide the best possible amount of air flow across the heatsink
In addition to these two factors, the heatsink must be designed in a such way that good thermal transfer is possible inside the heatsink (meaning that the heat can easily travel from the lower part of the heatsink, that is in contact with the CPU, to the fins, where the actual heat dissipation takes place). The part of the heatsink that is in contact with the CPU must be very flat in order to allow good thermal transfer. But even if the surface appears to be perfectly flat, there will still be small air gaps in the contact area between CPU and heatsink. Therefore, a thermal interface material, like thermal compound or a thermoconductive pad must be used.
So, in order to design an efficient heatsink, a solution would be to make it as big as possible, and add a very powerful fan. Another solution would be to let it have very fine fins, and use a clever design that allows the airflow from the fan to travel easily through the heatsink - by using a heatsink design that avoids turbulence and high air pressures inside the cooler. Of course, the ideal solution would be the combination of both solutions
The Material
Almost all heatsinks are made of aluminum. Why? The low cost and great mechanical characteristics make it very suitable for producing heatsinks. Generally, a pure metal has better thermal conductivity than an alloy. However, most heatsink manufacturers use aluminum alloys because of their better mechanical characteristics.
Many people wonder why copper isn't widely used for heatsinks - copper has a thermal conductivity that's almost twice as high as the thermal conductivity of aluminum (393 W/mK, as opposed to 221 W/mK). However, the performance of a heatsink doesn't only depend on the thermal conductivity of the material, so a copper heatsink certainly won't be twice as efficient as a heatsink made of aluminum. Therefore, the better thermal characteristics of copper do not justify the significantly higher cost and other considerations (rigidity, weight). Also, copper is not very suitable for extrusion (which is the preferred production method for heatsinks - see page 3). However, there are some heatsink models that are made of copper and aluminum. Here, usually the base plate is made of copper (or has a copper inlay), and the fins are made of aluminum.
The color
"A black object radiates the best - so all heatsinks should be black". True? Not really. Remember, most of the heat is dissipated using forced convection - and for this effect, the color is irrelevant. When doing a comparison test of two otherwise identical heatsinks with a different color, the measured performance difference is usually negligible. The main reason why heatsink manufacturers anodize their heatsinks is to make them look more attractive. Heatsinks exist in a variety of colors - black, silver, but also blue, green, gold, and red. For the performance, it doesn't make any major difference.
The production method
Different heatsink manufacturers
have come up with many different production methods. Let's have a look at
some of the popular heatsink designs:
Extruded
heatsink
![]() |
"Folded
fin" heatsink |
"Bonded
fin" heatsink |
Die-cast
heatsink |
Cold
forged heatsink |
Milled
/ cut heatsink |
- Extrusion is
the most popular production method for heatsinks. It is inexpensive, and
quite fine structures can be created using this production method. The liquid
aluminum is pressed through a form, so that a long stick with the shape
of the heatsink is created. After this "heatsink stick" stick has cooled
down, it is cut into pieces the size of the heatsink. However, there are
certain limitations with this production method. For example, a heatsink
shape like the one shown in the fourth image could not be produced with
this method.
- Folded fin design:
Here, the fins are made of a thin metal plate, which is folded, and bonded
onto a base plate. The advantage is that the fins are hollow, so they have
a bigger surface and allow better airflow (and thus better cooling). Using
this design, light, compact, and still very efficient coolers can be designed.
The disadvantage is that heatsinks with folded fins are more expensive to
produce, and therefore only a few manufacturers offer coolers using this
design.
- Bonded fin design:
This design is very similar to the "folded fin design", except that here,
many smaller metal plates are bonded onto the base plate, instead of one
large folded plate.
- Die casting:
This production method gives the heatsink designer a lot of freedom, and
allows for certain heatsink shapes that cannot be produced using extrusion.
However, the fins of a die cast heatsink cannot be very fine.
- Cold forging:
This is a relatively exotic production method. It's included here because
a very popular heatsink, the Alpha PFH6035MUC, is produced using this method.
This technology is very suitable for heatsinks with many small pin fins.
- Milling: Like cold forging, this production method is quite unusual for heatsinks. It's included in the chart because the heatsinks by HP PolarLogic are produced this way. Milling leaves the heatsink designers a lot of freedom, too, but it is expensive.
Of course, this is not
an exhaustive list, but almost all CPU heatsinks available on the market today
are produced with one of the above production methods.
Almost all CPU heatsinks require a fan, and in your computer case, there's at least one fan, usually two, even three or more. But when buying a fan, which factors should you consider?
The bearing system
Two kinds of fans are being used on CPU heatsinks: Ball Bearing, and Sleeve Bearing fans.
Sleeve bearing fans are usually less expensive and often quieter, but they are often less reliable. The cheapest kind of sleeve bearing simply consists of a ring made of a porous material, dipped in a lubricant. The fan motor's shaft rotates inside this ring, and is lubricated by the lubricant stored inside the porous material.
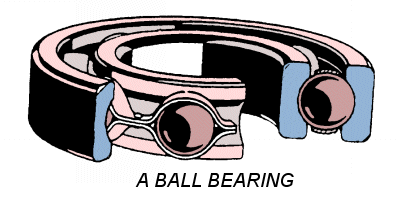
Ball bearing fans are a bit more expensive, and sometimes also louder, but they are generally more reliable. Just in case you're not familiar with bearing types: "Ball bearing" means that the rotating shaft is surrounded by tiny balls, which allow smooth rotation with hardly any wear and tear.
Note that if the sticker on the fan says "Ball bearing", then you'll often get a fan that uses both ball bearings and sleeve bearings. A fan needs two bearings, and the popular 50x10mm "ball" bearing fans that come with many heatsinks are usually fans with one ball bearing and one sleeve bearing. Larger fans (60x25mm and up) sometimes have two ball bearings - they are often referred to as "two ball" or "dual ball bearing" fans.
Generally, I would highly recommend buying only ball bearing fans (or dual ball bearing fans in the case of larger fans). Cheap sleeve bearing fans usually fail after only six months or less, whereas high quality ball bearing fans have a very high MTBF (Mean Time Between Failure). But some fan manufacturers also offer high quality sleeve bearing fans with Teflon(tm) bearings; these are just as reliable as ball bearing fans, and quieter - but also quite expensive.
Some words on noise
High airflow always creates noise - this cannot be avoided. For this reason, even a very high quality fan can be quite loud. However, in the case of a good fan, most of the noise it creates comes from the air turbulence, and not from the fan motor. Fan vibrations are a sign of poor quality. If you hold the fan in your hand, you should not feel any significant vibrations.
A larger fan that spins at a lower speed will be less noisy than a smaller fan spinning at a high speed, even if the two provide the same amount of airflow. So, the rule "bigger is better" also applies to fans.
How to specify fan performance
The most common unit for specifying airflow is CFM - Cubic Feet per Minute. In countries where metric system is more widely used, the unity m^3/min (cubic meters per minute) is also common. A conversion table for airflow units can be found here. In addition to this, the air pressure a fan creates can be measured (unlike CFM or m^3/min, this value does not depend on fan size).
50x10mm CPU fans usually move up to 10 CFM, high speed 50x10mm fans with 6000 rpm even more. 60x25mm fans commonly move between about 20 and 30 CFM, and 80x25mm around 30 to 40 CFM. 120mm fans can reach CFM values of over 100 CFM.
Remember, that, when buying a fan, you'll always have to chose between high performance and low noise. The goal is to find a good compromise.