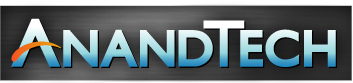
Original Link: https://www.anandtech.com/show/452
Heatsink Guide - AnandTech Heatsink Testing Methodology
by Tillmann Steinbrecher on January 21, 2000 11:55 PM EST- Posted in
- Guides
Before publishing the upcoming Athlon heatsink comparison test, here's a short overview of the testing methodology used for the heatsink tests on AnandTech.
Each heatsink test consists of two parts: A test under real-world conditions using an actual Athlon CPU, and a test with a simulator, which is a artificial heat source that simulates the heat emission of a CPU.
The test under real-world conditions is used to judge about factors like ease of installation, motherboard compatibility, and actual overclocking results. For this test, an ASUS K7M Rev. 1.04 Athlon motherboard is being used, along with an Athlon-650 CPU. The case used is an ASUS T-10A, the power supply a Sunny Technologies CWT-300ATX (which is identical to the Antec PP-303X, which showed the best stability in the AnandTech power supply comparison). For the overclocking test, a FreeSpeed Athlon overclocking card is being used however any Athlon overclocking device will work. Temperature measurements are also made during this test, just to verify that the temperature readings obtained with the simulator really represent performance under real-life conditions.
The test with the simulator is used to judge about the heatsink's cooling performance. You might wonder why we're not using an actual CPU for the temperature measurements. Well, for one reason: Precision. When using an actual CPU as a heat source, it is hardly possible to measure exactly how much heat is emitted to the heatsink. All you could do is measure the power usage of the entire motherboard, with CPU and extension cards. In addition, the CPU power usage depends on the CPU's operating state, different combinations of instructions result in different power usage. There are simply too many variables to consider, the result is less than ideal precision.
Many heatsink manufacturers are also using heaters instead of CPUs for their internal tests, for obvious reasons.
So, the conclusion is that a suitable test device for the heatsink test was needed. This device must have the following characteristics:
• The shape of the simulator's contact area to the heatsink must be identical to the actual CPU.
• The heat emission of the heat source must be perfectly constant - e.g. not depend from the temperature, time, or other factors (therefore, Peltier elements are not very suitable as a heat source).
To meet these two requirements, the simulator consists of a thermal transfer plate, taken from a Athlon CPU, and two resistors as the heat source, which have a perfectly constant power usage.
Resistors?
Many people think of tiny little sticks with colorful stripes when they hear
this word. But not all resistors are that small, and the ones chosen for the
»simulator« are rather large ones, as you can see on the image to the right.
Two 3.9 Ohm resistors with a tolerance of only 1% are being used for the simulator (the same kind of resistor is used in some high end amplifiers, for example). They are powered with 12V, which results in a total heat emission of 73.84 Watts (36.92 Watt per resistor, as you can easily calculate using the formulas U=R*I and P=U*I).
Close to 74 Watts power dissipation - that's quite a lot; more than any current x86 CPU consumes. But with a higher thermal load, performance differences between different heatsinks will become more obvious, and this is the reason why the simulator has such a high wattage.
The two resistors and the thermal sensor are glued to the SECC1 thermal transfer plate using thermoconductive epoxy.
From the front side, the simulator looks like an actual Athlon CPU...
... but on the back, the two resistors have replaced the Athlon CPU core.
The thermal sensor is located between the resistors.
Between the CPU and the heatsink, a thermal compound with a thermal resistance of 2.0 W/mK is applied. Some heatsinks come with a preinstalled thermal pad which should normally replace thermal compound; this pad is removed before testing. This is supposed to be a heatsink comparison, and not a thermal interface material comparison, and therefore all heatsinks are tested with the same thermal interface material.
Each heatsink test is run for 20 minutes. The published temperature reading is the maximum temperature the simulator has reached during this period.
Test results achieved using this test setup are perfectly reproducible. If you'd like to verify our testing, or if you'd like to see how your self-made heatsink/fan combo performs compared to the heatsinks tested on AnandTech, then you can go to an electronics store, buy two high performance 3.9 Ohm resistors, and glue them on a SECC1 thermal plate (e.g. from an old P2 CPU, if you don't want to open an Athlon just for that purpose) using thermoconductive epoxy. Keep in mind that the your measurements might differ slightly, because of the different interface materials - chances are that you'll be using a different thermal compound and a different thermal epoxy.